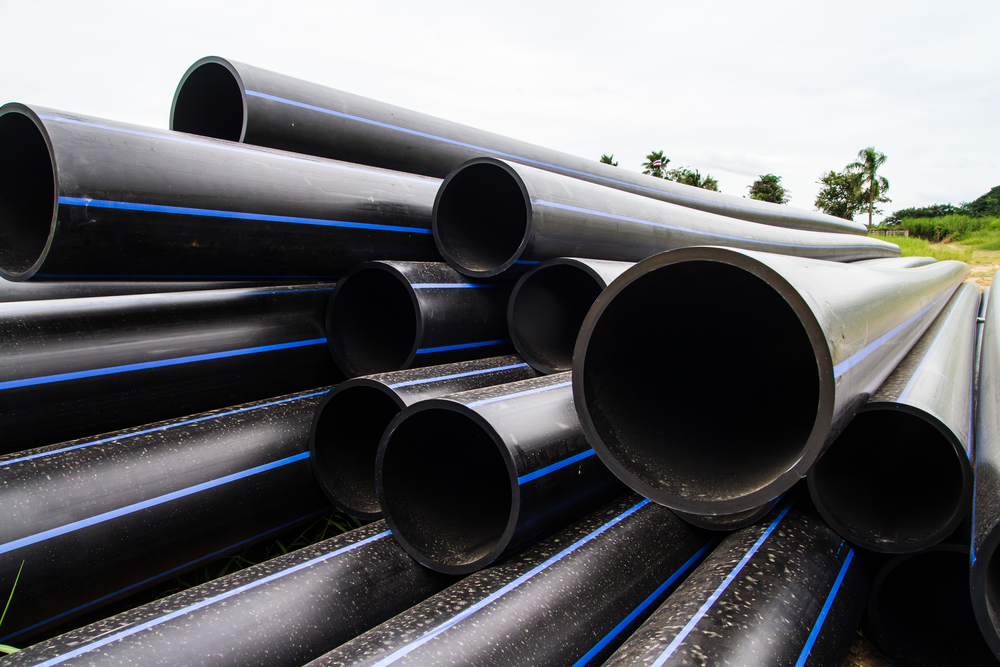
Working in a factory can be tough, not just for workers but for the pipes that carry all sorts of liquids and gases. These pipes must be resilient enough to handle bumps, scrapes, and even boiling or freezing substances that flow through them. Some factories even use chemicals that could damage regular pipes! So, what kind of pipes do these factories use? One popular choice is High-Density Polyethylene, or HDPE pipes and fittings. They’re known for being extremely durable, but why exactly are they ideal for rough and tumble manufacturing industries? This blog post will explain what HDPE pipes and fittings are made of, why they’re so solid, and why they can be the perfect choice for your next factory project.
Why Are HDPE Pipes Suitable for Harsh Industrial Environments?
HDPE pipes and fittings are suitable for harsh industrial environments due to their high durability and resistance to corrosion, chemicals, and abrasion. They are capable of handling severe temperatures and pressures and ensure smooth operation in harsh conditions without degradation or the need for frequent maintenance.
Several reasons why HDPE pipes and fittings are suitable for harsh industrial environments:
- Durability: HDPE pipes and fittings withstand harsh conditions, including chemicals and abrasion, ensuring long-term performance.
- Corrosion Resistance: They resist corrosion from chemicals and soil, maintaining integrity in aggressive industrial settings.
- High-Temperature Tolerance: HDPE pipes handle extreme temperatures without degradation, crucial for industrial operations.
- Flexibility: They adapt to ground movement and seismic activity, reducing the risk of fractures or leaks.
- Low Maintenance: HDPE pipes require minimal upkeep, reducing downtime and operational costs in industrial environments.
Are HDPE Pipes Suitable for Carrying Hazardous Materials?
HDPE pipes and fittings are ideal for carrying dangerous substances. They have high chemical resistance, which prevents interactions with the delivered compounds and ensures safe transportation. The smooth internal surface of HDPE pipes reduces the risk of blockages and the formation of hazardous contaminants. Also, HDPE pipes are impermeable, which eliminates leaks and contamination. Their strong structure provides a secure channel for hazardous materials, which makes them an effective alternative for industries handling such substances.
How Do HDPE Pipes Manage Wastewater in Industrial Facilities?
HDPE pipes and fittings influence wastewater in industrial facilities effectively due to their excellent qualities. They are extremely resistant to chemicals and abrasion, which allows them to withstand the diverse and frequently corrosive character of industrial effluent. The smooth internal surface reduces friction, which allows easy passage of wastewater and reduces the risk of clogs. The flexibility and strength of HDPE pipes make them appropriate for underground installation, where they are capable of bearing soil movements and severe loads without sacrificing performance.
How Do HDPE Pipes Improve Industrial Process Efficiency?
HDPE pipes enhance industrial process efficiency because they offer reliable fluid transmission. Their smooth internal surface reduces friction, which leads to more efficient flow and less energy consumption. HDPE’s durability and corrosion resistance also helps to ensure uninterrupted operation, reducing downtime and maintenance costs.
Here’s how HDPE pipes and fittings improve industrial process efficiency:
- Enhanced Flow Dynamics: HDPE pipes facilitate smooth flow, reducing friction and energy consumption in industrial processes.
- Corrosion Resistance: They withstand corrosive materials, ensuring long-term reliability and reducing maintenance needs.
- Leak-Free Performance: HDPE fittings provide secure joints, minimizing leaks that can disrupt industrial operations.
- Flexibility: These pipes adapt to ground movement, preventing damage and maintaining continuous operation.
- Cost Efficiency: HDPE’s durability and low maintenance requirements lower overall operational costs, improving efficiency in industrial processes.
How Do HDPE Pipes Compare to Metal Pipes in Industrial Settings?
HDPE pipes and fittings offer several advantages over metal pipes in industrial settings:
- Corrosion Resistance: HDPE pipes are highly resistant to corrosion from chemicals and soil, unlike metal pipes which may corrode over time.
- Lightweight: HDPE pipes are lighter than metal pipes, which makes them easier to transport, handle, and install in industrial settings.
- Flexibility: HDPE pipes have flexibility, which allows them to withstand ground movement and seismic activity better than rigid metal pipes.
- Smooth Interior: HDPE pipes have a smooth interior surface that promotes efficient flow and reduces the risk of blockages compared to metal pipes.
- Longevity: HDPE pipes have a longer service life and require less maintenance than metal pipes, contributing to cost savings over time in industrial applications.
What Benefits Do Flexible HDPE Pipes Offer in Harsh Industrial Settings?
Flexible HDPE pipes and fittings provide multiple benefits in harsh industrial settings:
- Shock Absorption: Their flexibility allows them to absorb shocks and vibrations, preventing damage from external forces.
- Ease of Installation: Their lightweight and flexible nature makes them easier to install, even in difficult-to-reach areas.
- Durability: HDPE pipes maintain their structural integrity in extreme temperatures and harsh environments.
- Chemical Resistance: They resist a wide range of chemicals, ensuring safe and efficient fluid transport.
- Cost Savings: Reduced risk of damage and lower maintenance requirements result in significant cost savings over time.
How Can Blockages in HDPE Pipes be Prevented in Industry?
Preventing blockages in HDPE pipes and fittings in industrial settings involves several measures:
- Regular Inspection: Conduct frequent inspections to detect potential blockages early.
- Proper Waste Disposal: Dispose of waste materials properly to prevent buildup in HDPE pipes.
- Flow Monitoring: Monitor flow rates to detect any irregularities that may indicate impending blockages.
- Clearing Debris: Implement procedures to clear debris from pipes and drainage systems regularly.
- Use of Filters and Screens: Install filters and screens to trap debris and prevent it from entering HDPE pipes.
What Are Common Issues With HDPE Pipes in Industry and Their Solutions?
Common issues with HDPE pipes and fittings in the industry and their solutions include:
- Joint Failures: Ensure proper welding techniques and use quality fittings to prevent joint failures.
- Abrasion: Use abrasion-resistant coatings or sleeves to protect pipes from wear and tear in abrasive environments.
- Chemical Attack: Choose HDPE pipes with appropriate chemical resistance for the specific industrial application.
- Pressure Surges: Install pressure relief valves to manage pressure surges and prevent pipe damage.
- Installation Errors: Ensure trained personnel handle the installation to avoid issues related to incorrect installation.
Enhancing Industrial Environments with Adamjee HDPE Pipes
Adamjee DuraBuilt is a popular HDPE pipe manufacturer in Pakistan. We focus on making high-quality HDPE pipes and fittings that are resistant to harsh industrial environments. Our products are known for their durability, chemical resistance, and flexibility, which makes them suitable for various industrial applications. With a commitment to quality and innovation, Adamjee DuraBuilt provides reliable solutions that enhance the efficiency and performance of industrial systems.
Wrap Up: Enhancing Industrial Efficiency with HDPE Pipes
HDPE pipes and fittings are ideal for severe industrial situations. Their durability, chemical resistance, and flexibility provide consistent performance and long-term efficiency. HDPE pipes are superior to previous materials in terms of blockage prevention, hazardous material handling, and process efficiency. With regular maintenance and installation, HDPE pipes can improve the efficiency and reliability of industrial drainage systems, providing cost-effective solutions for multiple industrial uses.
Dive into more insightful blogs available here